Etched Metal Fuel Cell Plates are Thinner, Stronger, and Offer Superior Electrical Performance
ETCHED METAL FUEL CELL PLATES PROVEN BENEFITS
Photo Etched metal plates are ideal for applications requiring good volumetric power densities, long life, and robust performance. Photo etching metal offers fuel cell designers unique time-saving and cost advantages:
- No expensive tooling or time consuming mold making.
- Multiple channel levels are etched onto the fuel cell plate.
- Smooth surfaces are burr and stress-free.
- Carbon coating is available.
- High volume, rapid prototyping is available through our Innovation Center.
Compared to graphite, Stainless Steel and Titanium bipolar flow field plates are more robust with improved volumetric power density. These plates for PEM fuel cells are extremely corrosion resistant and offer many advantages:
- Where space is limited, they are thinner, producing a shorter stack.
- Metals offer superior electrical and heat conductivity to non-metal solutions.
- For mobile applications, metal plates are less fragile and able to withstand mechanical impact.
- For long-life applications, Stainless Steel and Titanium extend life time and improve electrical performance.
Robotic spray coating applies conductive coatings to any metal product
At Tech Etch, we’ve developed a system to coat our metal products with a conductive coating with ease. Whether you need coatings for fuel cells, battery current collectors, or other energy storage devices, our coating system can provide the solution you need most.
Conductive coatings improve battery performance via better electrical contact. They also provide improved oxidation and corrosion protection, resulting in longer shelf life and reduced leakage. Our robotic coating equipment features an articulated head that ensures a uniform coating over the metal. The system can use either epoxy or water-based coatings.
How PEM fuel cells work
Fuel cells gather chemical energy and convert it into electrical energy. They use hydrogen as the fuel and oxygen to convert. This results in electricity, as well as water and heat as by-products. The Proton Exchange Membrane (PEM) helps transmit protons from one side to the other. PEM fuel cells can operate at much lower temperatures than other fuel cells, around 90 degrees Celsius.
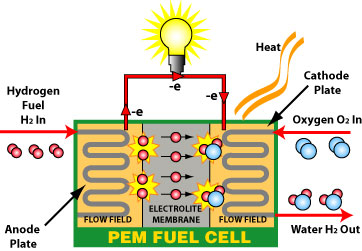
A fuel cell has an anode and a cathode as its electrodes, separated by a polymer membrane. The electrodes are coated on a single side with a catalyst. Hydrogen goes into the anode and air enters the cathode.
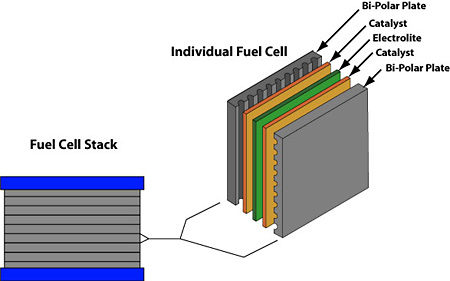
Combine these two with the catalyst and the hydrogen splits into two protons and two electrons.
The electrons flow through the circuit and create a current. The protons travel through the membrane, combine with the electrons, and create by-products of water and heat. With enough fuel cells in place, useful electricity can be produced. They make for a great source of power due to their efficiency, low emissions, quiet operation, and ability to be produced in a variety of sizes.